Porosity in Welding: Identifying Common Issues and Implementing Ideal Practices for Prevention
Porosity in welding is a pervasive concern that usually goes undetected up until it triggers considerable problems with the stability of welds. In this conversation, we will certainly discover the essential variables contributing to porosity development, analyze its harmful effects on weld efficiency, and go over the finest techniques that can be adopted to decrease porosity occurrence in welding processes.
Usual Reasons For Porosity
An additional constant offender behind porosity is the existence of impurities externally of the base steel, such as oil, oil, or corrosion. When these impurities are not successfully eliminated before welding, they can evaporate and come to be trapped in the weld, causing problems. Making use of dirty or damp filler products can present contaminations right into the weld, adding to porosity problems. To reduce these usual reasons for porosity, detailed cleansing of base metals, proper securing gas selection, and adherence to ideal welding criteria are necessary techniques in accomplishing premium, porosity-free welds.
Influence of Porosity on Weld High Quality

The existence of porosity in welding can substantially jeopardize the structural integrity and mechanical buildings of bonded joints. Porosity creates voids within the weld steel, weakening its general stamina and load-bearing capability. These voids serve as anxiety focus points, making the weld extra vulnerable to cracking and failure under applied lots. Furthermore, porosity can reduce the weld's resistance to rust and various other ecological variables, additionally lessening its long life and efficiency.
One of the key repercussions of porosity is a reduction in the weld's ductility and company website sturdiness. Welds with high porosity levels often tend to show lower impact stamina and lowered capacity to flaw plastically before fracturing. This can be specifically concerning in applications where the bonded parts undergo dynamic or cyclic loading conditions. Porosity can impede the weld's capacity to efficiently send pressures, leading to early weld failure and potential security threats in important frameworks. What is Porosity.
Finest Practices for Porosity Prevention
To improve the architectural honesty and top quality of welded joints, what particular steps can be implemented to minimize the event of porosity during the welding procedure? Using the appropriate welding strategy for the specific material being welded, such as changing the welding angle and gun setting, can further stop porosity. Normal assessment of welds and instant remediation of any problems recognized throughout the welding procedure are crucial techniques to protect against porosity and produce top notch welds.
Relevance of Correct Welding Methods
Applying appropriate welding methods is critical in guaranteeing the structural integrity and quality of bonded joints, building upon the foundation of directory effective porosity avoidance actions. Extreme warm can lead to enhanced porosity due to the entrapment of gases in the weld pool. In addition, making use of the proper welding specifications, such as voltage, present, and travel speed, is essential for accomplishing audio welds with marginal porosity.
Furthermore, the option of welding procedure, whether it be MIG, TIG, or stick welding, need to align with the details requirements of the job to make sure optimum results. Correct cleansing and preparation of the base metal, along with choosing the best filler material, are additionally important elements of efficient welding methods. By sticking to these best methods, welders can minimize the danger of porosity formation and produce top quality, structurally sound welds.
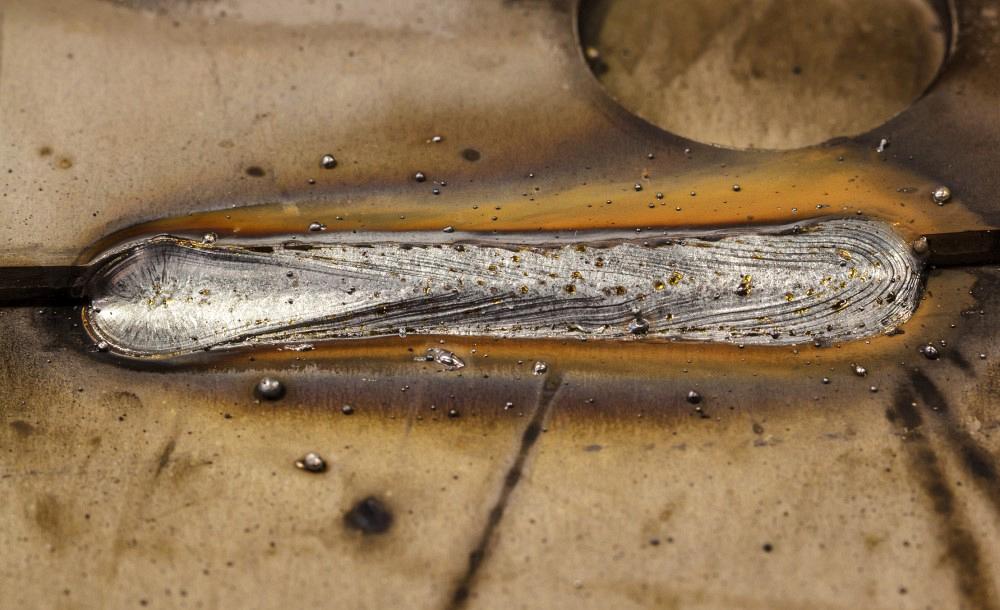
Testing and Quality Control Measures
Checking procedures are crucial to find and avoid porosity in welding, guaranteeing the look at more info strength and sturdiness of the final product. Non-destructive screening approaches such as ultrasonic screening, radiographic screening, and aesthetic examination are generally utilized to recognize prospective defects like porosity.
Post-weld assessments, on the other hand, assess the last weld for any defects, including porosity, and validate that it fulfills defined criteria. Implementing a detailed quality control strategy that includes extensive testing treatments and assessments is extremely important to decreasing porosity issues and making certain the general high quality of bonded joints.
Final Thought
In verdict, porosity in welding can be a common problem that affects the quality of welds. By determining the typical reasons of porosity and applying ideal methods for avoidance, such as proper welding strategies and screening procedures, welders can make certain top quality and reputable welds. It is crucial to prioritize avoidance approaches to decrease the incident of porosity and keep the stability of bonded structures.
Comments on “Exactly how to Identify What is Porosity in Welding and Improve Your Strategy”